Импортозамещение — замещение импорта товарами, произведёнными внутри страны. Несмотря на глобальный характер обмена товаров и услуг, как говорят американцы, – «главные вещи делайте сами», сколько бы они не стоили. Вспомним из У.Шекспира: «Коня, коня, полцарства за коня!».
В нефтегазовом комплексе России в условиях санкций проблема импортозамещения продукции машиностроения стоит чрезвычайно остро. История проблемы началась задолго до санкций и была запущена реформами 1990‑х гг., сформировавшими экпортозамещение машин сырьем. Недальновидно, но приятно бороться с симптомами не устраняя причин. До сих пор результаты реформ игнорируются («курс реформ будет неизменным») или обсуждаются максимум «для служебного пользования». Озвучиваемая проблема импортозамещения – прямое следствие результатов реформы деиндустриализации, разработанной и объявленной еще академиком А.Н. Яковлевым.
Предполагаемая Правительством РФ реиндустриализация страны сразу обострит проблему обеспечения промышленной безопасности в РФ. Существенно изменится ситуация с аварийными опасностями и при реализации объявленных программ импортозамещения машиностроительной продукции в нефтегазовом комплексе. Если дело дойдет до их реализации, то встанет и другая аварийно-опасная проблема экспортозамещения сырья на машины (сначала необходимо решить проблему экспортовозмещения энергии и сырья для внутреннего производства в РФ). В любом случае экспортируемые сейчас энергоресурсы нужны для запуска индустрии (в т.ч. и импортозамещения), и эту "дополнительную" энергию еще нужно суметь превратить не только в товары для импортозамещения, но и обуздать, не допустив "дополнительных" промышленных аварий - т.е. обеспечить промышленную безопасность при реиндустриализации (импортозамещение машин - экспортовозмещении энергии и сырья).
Чтобы грядущий переход не стал аварийно-болезненным необходимо знать общее состояние, тенденции и фоновые показатели опасности промышленных аварий. Рассмотрим* этот вопрос на примере нефтедобывающей промышленности (станового хребта российского ТЭК и экономики РФ).
* Далее использованы официальные статистические данные, а также материалы А.И. Гражданкин, С.Г. Кара-Мурза. Белая книга: промышленность и строительство в России 1950–2014 гг. /Центр изучения кризисного общества. М.: Научный эксперт; М.: ТД Алгоритм, 2016. - 224 с.
Известно, какое значение для смягчения нынешнего положения России, а также для накопления средств для выхода из кризиса и будущего развития (через программы экспортовозмещения), имеет добыча и переработка углеводородного сырья. Однако в добыче приближается критический период истощения тех месторождений, которые были разведаны и обустроены в советское время, хотя многие из них пока законсервированы, а эксплуатируются лишь наиболее рентабельные.
Вести такую разведку мог только мощный государственный научно-производственный комплекс. Приватизация промышленных предприятий и демонтаж отраслевой научно-технической системы парализовали геологоразведку. Сегодня остро необходимо расширение геологоразведки (в том числе и на шельфе[1]), однако с начала реформы происходило быстрое свертывание разведочного бурения на минеральные ресурсы.
[1] Россия уже "опоздала с импортозамещением оборудования на шельфе" и без "интеграции с другими странами, имеющими опыт в этой сфере", не обойтись, заявил 22.09.2015 вице-премьер Александр Хлопонин (http://kommersant.ru/doc/2815995)
При сохранении курса реформ 1990-х гг. в перспективе возможности значительного роста добычи малы, т.к. с конца 1980‑х гг. глубокое разведочное бурение на нефть и газ резко сократилось (рис.1).
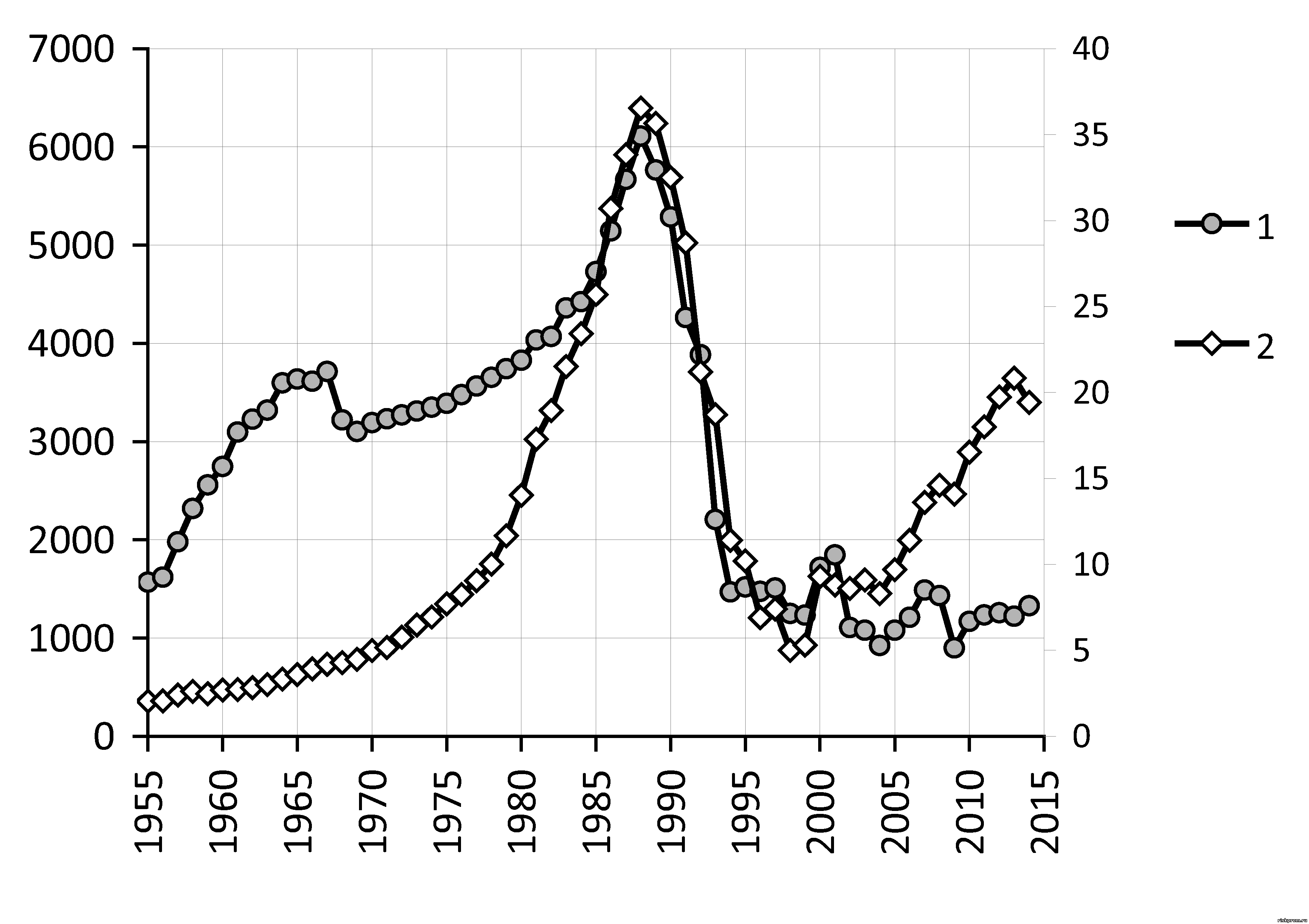
Рис. 1. Бурение на нефть и газ в РСФСР и РФ, тыс. м:
1 – глубокое разведочное (левая шкала, тыс. м)
2 – эксплуатационное (правая шкала, тыс. км)
По данным Минпромторга РФ оборудование, использующееся в России для добычи нефти и газа, изношено (буровое – на 50%, трубопроводное – на 65%). В последние 10-15 лет российские нефтегазосервисные компании в несколько раз больше тратили на поддержание текущей эксплуатации, чем на расширение производства, и результатом стало то, что на 2012 г. только 17% буровых установок изготовлены после 2000 года, а 63% – в 1980-х годах. В Минпромторге РФ считают, что есть тенденция к почти полному вытеснению российских производителей оборудования с внутреннего рынка[1]. По данным Ростехнадзора по состоянию на 2014 г. общее количество бурового оборудования в составляет – 2265 единиц из него, с нормативным сроком эксплуатации – 825 (36,6%), с истекшим сроком эксплуатации – 281 (12,4%), с продленным сроком эксплуатации – 1159 (51,2%)[2].
Многократно большие объемы бурения требуются при освоении разведанных месторождений. До 1991 г. проведение этих работ было обеспечено в том числе тем, что Россия располагала высокоразвитым производством турбобуров[3].
[1] Бурите отечественным. "Коммерсантъ", №231 (5016), 06.12.2012
[2] Информация о состоянии бурового оборудования в организациях топливно–энергетического комплекса. Ростехнадзор, 2015 (http://gosnadzor.ru/activity/analiz/neftegaz)
[3] Турбобур был изобретен М.А. Капелюшниковым, С. М. Волохом и Н. А. Корневым и запатентован в сентябре 1922 года. Он был представлен на выставке в США, и показал скорость бурения на 60% выше, чем известные роторные установки, при расходе энергии в три раза меньше. Производство турбобуров было начато в 1925 г. в Баку. Эта машина чрезвычайно эффективна: средняя механическая скорость проходки составляла более 50 м/ч, проходка на одну буровую бригаду – более 100 тысяч метров в год. Применение турбобуров в Сибири позволило в сжатые сроки построить огромное число скважин на месторождениях нефти и газа. По советским лицензиям было налажено производство на Западе, в том числе в США. сегодня до 70% объемов бурения производится винтовыми забойными двигателями (ВЗД)
Это производство было в полном смысле слова ликвидировано в первые же два года реформы, и к 1999 г. оно сократилось по сравнению со стабильным уровнем 1980-х гг. в 130 раз, а еще через десять лет к 2009 г. - в 560 раз. Динамика этого процесса показана на рис. 2.
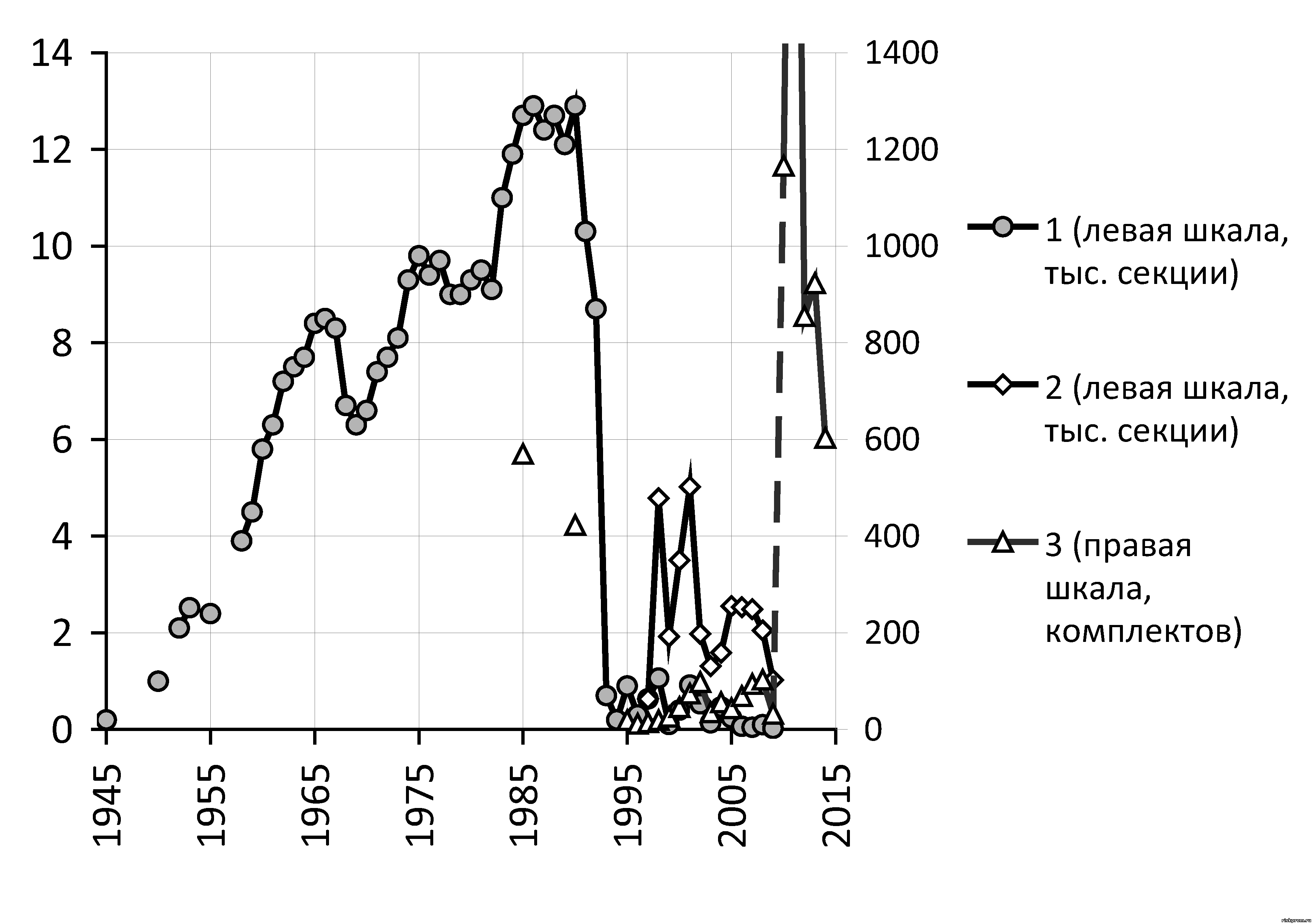
Рис. 2. Производство бурового оборудования в РСФСР и РФ:
1 – турбобуры, тыс. секций (после 2009 г. данные Росстатом не публикуются);
2 – винтовые забойные двигатели, тыс. секций (после 2009 г. данные Росстатом не публикуются);
3 – установки буровые для эксплуатационного и глубокого разведочного бурения, комплектов
(с 2009 г. изменена методика учета; в 2011 г. – 2817 комплектов)
В бурении быстро происходит смена технологических укладов, деиндустриализация негативно повлияла и на процесс освоения инноваций. В начале 2010-х гг. до 70% объемов бурения на нефть и газ производится винтовыми забойными двигателями (ВЗД). В 1997 г. было произведено 0,6 тыс. секций ВЗД, в 2000 г. – 3,5, в 2005 г. – 2,5, в 2009 г. – 1,024 тыс. секций ВЗД (после 2009 г. данные по ВЗД Росстатом не публикуются). В десятки раз в 1990 ‑х гг. сокращено производство установок буровых для эксплуатационного и глубокого разведочного бурения (1990 г. – 423, в 1996 г. – 12 комплектов). С 2009 г. изменена методика учета их производства: по новым данным, например, в 2009 г. было произведено не 32, а 1800 комплектов установок буровых. Однако тенденция сокращения выпуска буровых установок сохраняется и по новой методике учета: только за 2011-2014 гг. их производство сократилось в 4,7 раз.
Предполагаемый рост разведочных работ сразу обострит проблему обеспечения промышленной безопасности в нефтегазодобыче, существенно изменится ситуация с аварийными опасностями и при реализации программ импортозамещения машиностроительной продукции в нефтегазовом комплексе. Чтобы грядущий переход не стал аварийно-болезненным необходимо знать общее состояние тенденции и фоновые показатели опасности аварий в нефтедобывающей промышленности
Возникновение и выявление известных и новых угроз техногенного и антропогенного характера на протяжении всей истории индустриальной культуры порождает необходимость разработки новых средств и способов предупреждения промышленных аварий, а на современном этапе позднего индустриализма - внедрение риск-ориентированного подхода для информационно-аналитического обеспечения и повышения эффективности обеспечения промышленной безопасности опасных производственных объектов.
Риск-ориентированный подход в обеспечении промышленной безопасности предполагает формирование актуальной «карты опасностей», как системы сбора, анализа и представления беспристрастной информации о текущей ситуации и прогнозирования опасностей промышленных аварий, в том числе об инцидентах, авариях, несчастных случаях и угрозах крупных промышленных аварий в системе поднадзорных опасных производственных объектов. «Карта опасностей» промышленных аварий, как система показателей негативных проявлений аварийности и травматизма в производственной деятельности, формируется в сопоставительном взаимодействии с данными о технико-экономическом состоянии промышленного производства, как правило, в отраслевом разрезе. Очевидно, что импортозамещение существенно отразится на «карте опасностей» промышленных аварий (повлияет смена поставщиков и изготовителей применяемых технических устройств и стандартов ее обслуживания в условиях сохранения соблюдений требований промышленной безопасности и возможных отступлений от них в рамках процедуры обоснования безопасности, - важно чтобы такое влияние не осталось безнадзорным).
Аварийность и травматизм – «теневая сторона» состояния промышленной деятельности. Кратко рассмотрим, что наблюдалось на «лицевой стороне медали» в нефтегазодобыче.
На начало 2015 г. в государственном реестре Ростехнадзором зарегистрировано 7287 опасных производственных объектов (ОПО) нефтегазодобычи, из них: 302 участка ведения буровых работ, 2338 фондов скважин, 361 участок предварительной подготовки нефти, 945 площадок дожимных насосных станций и насосных станций, 612 пунктов подготовки и сбора нефти, 125 парков резервуарных, 2066 систем промысловых (межпромысловых) трубопроводов месторождений протяженностью 341 707,35 км, 125 промысловых компрессорных станций, 270 участков комплексной подготовки газа, 7 стационарных морских платформ, 10 плавучих буровых установок.
Отдельные технико-экономические показатели работы организаций по добыче сырой нефти и нефтяного (попутного) газа представлены в таблице 1 (здесь и далее по официальным данным Росстата разных лет).
Таблица 1
Отдельные технико-экономические показатели работы
организаций по добыче сырой нефти и нефтяного (попутного) газа (1990-2013 гг.)
|
1990
|
1995
|
2000
|
2005
|
2010
|
2011
|
2012
|
2013
|
Объем добычи нефти (включая газовый конденсат), млн т
|
516
|
307
|
324
|
470
|
505
|
512
|
519
|
522
|
Добыча нефти по способам эксплуатации
скважин, в процентах от общего объема
добычи:
|
|
|
|
|
|
|
|
|
насосный
|
81,0
|
87,2
|
89,6
|
93,0
|
91,5
|
92,0
|
91,8
|
92,8
|
компрессорный
|
7,0
|
3,6
|
1,5
|
0,8
|
0,7
|
0,4
|
0,4
|
0,6
|
фонтанный
|
12,0
|
9,0
|
8,5
|
6,2
|
7,7
|
7,4
|
7,4
|
6,3
|
Среднесуточный дебит одной скважины, т
|
11,6
|
7,5
|
7,5
|
10,3
|
10,0
|
10,0
|
10,0
|
9,7
|
Эксплуатационный фонд скважин, тыс. шт.
|
139
|
143
|
151
|
151
|
158
|
159
|
164
|
164
|
Бездействующий фонд скважин, тыс. шт.
|
9,8
|
29,4
|
27,8
|
24,5
|
18,6
|
18,1
|
17,7
|
15,5
|
Удельный вес бездействующего фонда скважин в эксплуатационном фонде, процентов
|
7,0
|
20,6
|
18,5
|
16,2
|
11,8
|
11,4
|
10,8
|
9,5
|
Объем бурения на нефть, млн. м
|
|
|
|
|
|
|
|
|
эксплуатационного
|
32,7
|
10,2
|
9,3
|
9,7
|
17,2
|
18,0
|
19,7
|
20,9
|
разведочного
|
5,2
|
1,4
|
1,5
|
0,9
|
1,1
|
1,2
|
1,2
|
1,3
|
Средняя глубина законченных эксплуатационным бурением скважин, м
|
2280
|
2237
|
2309
|
2526
|
2734
|
2747
|
2763
|
2888
|
Проходка на одно долбление, м
|
160
|
147
|
144
|
204
|
365
|
430
|
358
|
501
|
Уровень использования нефтяного (попутного) газа, в процентах от общих ресурсов нефтяного (попутного) газа
|
80
|
81
|
80
|
76
|
76,7
|
75,6
|
75,9
|
79,5
|
Аварийная опасность нефтегазодобычи во многом определяется технологической спецификой данной производственной деятельности и зависит от ее масштаба и интенсивности, от динамики разведки и добычи, и особенно от резких переходных трансформационных процессов в отрасли. Опасность и угрозы промышленных аварий существенно и качественно различается в периоды роста, стагнации, падения и восстановления любой отрасли промышленности, хотя их абсолютные количественные параметры аварийности и травматизма могут представляться одинаковыми. В риск-ориентированном подходе «карта опасностей» промышленных аварий строится на основе данных о состоянии промышленного производства отрасли, ее кадрового и материально-технического обеспечения. В этом разрезе рассмотрим основные этапы становления и развития отечественной нефтегазодобычи.
За 1960-1970-е гг. в России был создан мощный нефтедобывающий комплекс, так что в 1980-е гг. добыча поддерживалась на уровне 550-570 млн т. К середине 1990‑х гг. объем добычи упал до 301 млн т в 1996 г., а затем, начиная с 2000 г., поднялся до 470 млн т – в 2005 г., до 505 млн т. – в 2010 г. и до 525 млн т – в 2014 г. При этом в 1991-2001 гг. происходило падение производительности труда в отрасли с 3,8 до 1 тыс. т добытой нефти на одного занятого в нефтедобыче работника. С 2002 г. положение стало выправляться. В расчете на одного работника в 2010-2014 гг. добыто 3,3-3,7 тыс. т нефти, т.е. почти восстановлен уровень 1990 г. в 3,8 тыс. т (рис. 3).
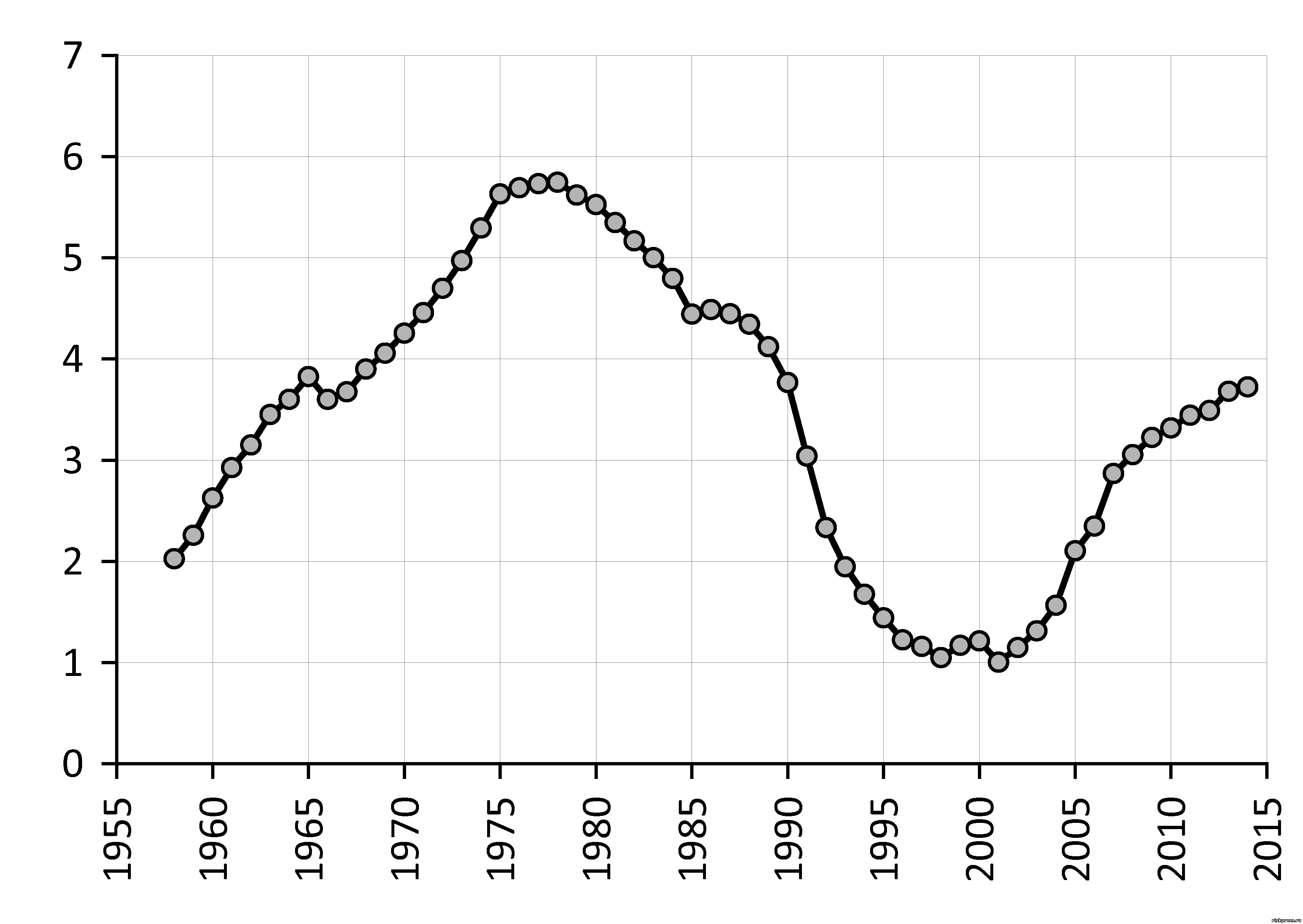
Рис. 3. Производительность труда в нефтедобывающей промышленности России, тыс. т добытой нефти на 1 работающего
В перспективе возможности значительного роста добычи малы, т.к. в начале 1990-х гг. глубокое разведочное бурение на нефть и газ резко сократилось (табл.1). В 1991-1998 гг. почти в 7 раз сократились объемы эксплуатационного бурения, к середине 2010-х гг. дореформенный уровень пока не восстановлен (табл. 1).
Бурение – одна из наиболее аварийно-опасных операций при добыче нефти и газа, поэтому восстановительный рост объемов бурения может в ближайшей перспективе сопровождаться и повышением абсолютных значений аварийности и травматизма в отрасли.
В посткризисные и переходные периоды в риск-ориентированном подходе эффективность обеспечения промышленной безопасности оценивается не только по абсолютному числу аварий и травм, но и по относительным показателям опасности аварий (на объем добычи или бурения, на число занятых, на производительность труда). Существенное влияние оказывают на аварийность и травматизм не только применяемые технологии, но и состояние используемого оборудования.
По данным Росстата особенно резко увеличился темп износа основных фондов нефтегазодобычи после 2010 г. (рис. 4) – к 2015 г. могут быть практически достигнуты максимальные исторические уровни по степени износа основных фондов. Износ основных фондов – еще не приговор наступления промышленных аварий, при условии адекватного степени износа обхождения и обслуживания технологического оборудования, в т.ч. минимизации резких переходных и нештатных пуск-остановочных режимов в процессе эксплуатации.
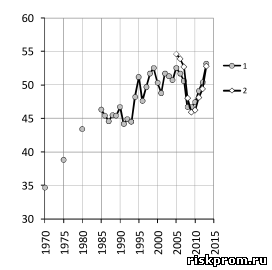
Рис. 4. Степень износа основных фондов в топливно-энергетических отраслях в РСФСР и РФ, %
1 – в топливной промышленности (с 2005 г. в добыче топливно-энергетических полезных ископаемых);
2 – в добыче сырой нефти и нефтяного (попутного) газа; извлечение фракций из нефтяного (попутного) газа
По данным Ростехнадзора доля импортного оборудования на предприятиях нефтегазодобычи в 2013 году составила 28,7%. По этому показателю наблюдается тенденция к снижению, к 2015 году по прогнозу он снизится на 1,1%. Разброс значений этого среднего показателя существенный, например, доля импортного оборудования подготовки и сбора нефти и нефтепромысловых трубопроводов, в том числе, запорной арматуры, в компании ОАО «АНК «Башнефть» составляет до 73% в ФАО «Тоталь РРР» - до 90%. Основными производителями импортного оборудования, эксплуатируемого на объектах российской нефтегазодобычи, являются США, Япония, Германия, Италия, Франция, Великобритания, на многих предприятиях эксплуатируется динамическое оборудование украинского производства.
Применение старого нефтепромыслового оборудования осуществляется в основном на стареющих месторождениях в Республике Татарстан, Республике Башкортостан, Чеченской Республике, Республике Ингушетия, Самарской области, Краснодарском крае, где эксплуатация нефтяных и газовых месторождений осуществляется с начала 1940-х гг. Старение и износ основных производственных фондов остается главной отраслевой проблемой для нефтегазодобывающих производств.
Объекты и технические устройства нефтегазодобычи, выработавшие нормативный срок службы и эксплуатируемые более 25 лет, по статистической отчетности территориальных органов Ростехнадзора составляют 48% от общего количества оборудования нефтегазодобычи.
Общее количество бурового и геофизического оборудования, эксплуатируемого на опасных производственных объектах нефтегазодобычи составляет – 2257 единиц (на начало 2015 г.) из них, эксплуатируются с установленным сроком эксплуатации – 812 (36%), с истекшим сроком эксплуатации – 290 (12,8%), с продленным сроком эксплуатации – 1155 (51,2%). 2071 единица (91,7%) бурового оборудования эксплуатируются на предприятиях ТЭК поднадзорных Северо – Уральскому, Западно - Уральскому, Средне – Поволжскому и Приволжскому управлениям.
Сравнительный анализ информации по состоянию бурового оборудования, представленный территориальными управлениями показывает, что 1445 единиц (64%) отработали свой установленный срок эксплуатации, из них 1155 (51,2%) прошли экспертизу промышленной безопасности с продлением сроков дальнейшей эксплуатации. Принимаются лишь меры по диагностике бурового оборудования, отработавшего установленный срок эксплуатации, с целью продления дальнейшей эксплуатации.
По данным Ростехнадзора на первое полугодие 2014 г. в выборке промысловых (межпромысловых) трубопроводов из 49,3 тыс. ед., протяженностью – 261,787 тыс. км, сроки их эксплуатации составляли:
менее 5 лет – 10 571 ед.(21,4%), 61,035 тыс. км (23,3%);
от 5 до 10 лет – 18 783 ед. (38,2%), 45,978 тыс. км (17,6%);
от 10 до 20 лет – 19 405 ед. (39,1%), 154,523 тыс. км (59%);
свыше 20 лет – 574 ед. (1,3%), 0,251 тыс. км (0,1%).
40% от общего количества (почти 60% по протяженности) промысловых и межпромысловых трубопроводов эксплуатируется со сроком от 10 лет и больше, что свидетельствует о низком темпе замены отработавшего установленный срок оборудования и трубопроводов. Не на всех предприятиях разработаны и согласованы перспективные среднесрочные программы по ревизии и замене устаревшего и отработавшего установленный срок эксплуатации оборудования и трубопроводов.
Замена оборудования вертикально-интегрированными компаниями производится в рамках капитального ремонта и реконструкции нефтегазодобывающих производств. Об интенсивности данных работ косвенно свидетельствуют оперативные данные Росстата: в 2014 г. из 3577 ед. введенных в действие нефтяных скважин, только 4 ед. были введены за счет реконструкции (при эксплуатационном фонде скважин в 164 тыс. ед.). В 2005 г. удельный вес полностью изношенных основных фондов в организациях добычи сырой нефти и нефтяного (попутного) газа составлял 24,1%, в 2010 г. – 20%, в 2013 г. – 23,5%. Аналогичный показатель для организаций добычи природного газа и газового конденсата в 2010 г. составлял 30,2%, а в 2013 г – 35,8%. В середине-конце 2000-х гг. выбытие изношенных основных фондов в российской нефтедобыче происходило примерно на треть быстрее, чем в первой половине 2010‑х гг.
Относительный уровень опасности смертельного травмирования в нефтегазодобыче может быть оценен по данным Росстата: в 2005 г. численность смертельно пострадавших в добыче полезных ископаемых составляла 0,279 на 1000 работающих, в 2010 г. – 0,274, в 2012 г. – 0,205, в 2013 г. – 0,182 погибших на 1000 работающих (в 2,3 раза выше среднероссийского уровня по всем видам экономической деятельности). В 2012 г. численность смертельно пострадавших в добыче сырой нефти и природного газа (вкл. предоставление услуг в этих областях) составляла 0,112 погибших на 1000 работающих (на 45% ниже, чем в среднем по добывающей промышленности). Однако эти данные в недостаточной степени показывают тенденции изменения причин возникновения и тяжести производственного травматизма, межотраслевые соотношения опасности травмирования работающих изменяются только с крупными технологическими новациями.
В области промышленной безопасности фиксируются и соответствующим образом расследуются несчастные случаи непосредственно связанные с отраслевой технологией выполнения работ (в общем производственном травматизме доминируют несчастные случаи в дорожно-транспортных происшествиях, «затирающие» непосредственные опасности производственной деятельности). Данные Ростехнадзора по смертельному травматизму на опасных производственных объектах (в отличие от производственного травматизма в промышленности) более акцентировано фокусируются на основных опасностях производственных объектов.
Основные тенденции динамики смертельного травматизма на опасных производственных объектах нефтедобычи представлены на рис. 5.
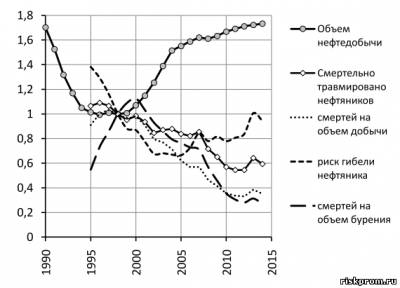
Рис. 5. Объемы добычи и показатели смертельного травматизма на опасных производствах нефтедобывающей промышленности России, условные индексы (1998 г. = 1)
В 1990-1999 гг. наблюдался резкий спад добычи нефти с 516 до 305 млн т, однако абсолютный смертельный производственный травматизм практически не снижался – находился на уровне 20-28 погибших/год, а относительный рос в 1991-1994 (с 5,2 до 8,8 смертей/100 млн т добытой нефти) и стагнировал в 1995-2000 гг. (на уровне ок. 7 смертей/100 млн т).
Кроме того с 1990 г. наблюдался резкий спад объемов наиболее аварийноопасных операции бурения на нефть: эксплуатационного – более чем в три раза (вплоть до 2002 г.) и разведочного – более чем в 5 раз (см. табл.1). Число аварий в отрасли снизилось к 2002 г. примерно в два раза. С возобновлением роста эксплуатационного бурения (~ в 2 раза от минимума 1996 г.) и при стагнации разведочного бурения в 1998-2014 гг. наблюдался рост (~1,5 раза) и затем стабилизация ежегодного числа аварий. Отметим, что частота аварий при эксплуатационном бурении в 3-4 раза ниже, чем при разведочном, а трудоемкость ликвидации – примерно в 1,5 раза.
Существенное снижение производительности труда к 2000 г. (рис. 3) и увеличение численности занятых в отрасли обусловливает снижение (почти 4-х кратное) удельного смертельного травматизма в 1991-2002 гг. Последующее восстановление роста (~3 раза) производительности труда в 2000-2013 гг. сопровождалось почти двукратным ростом риска гибели нефтяника (отношение число погибших на число работающих)– см. рис. 5.
Спад в нефтедобыче 1990-2000 гг. экстенсивно снизил и опасности промышленных аварий – с отставанием, но в целом уменьшалось абсолютное число погибших и количество аварий, снижался удельный смертельный производственный травматизм.
Оживление и бурный рост добычи нефти в 2000-2005 гг. при стагнации эксплуатационного и разведочного бурения сопровождались незначительным ростом числа аварий и некоторым снижением абсолютного числа погибших (происходила загрузка «омертвленных мощностей»). Относительный смертельный травматизм на 100 млн т добычи сократился на 40%, а риск гибели нефтяника – практически не изменился (ок. 7-8 смертей на 100 тыс. работающих).
В 2006-2014 гг. рост добычи нефти продолжился в несколько меньшем темпе, кроме того более чем вдвое выросли объемы эксплуатационного бурения. В этот же период абсолютное число смертельно травмированных сократилось еще почти на треть, а показатели удельного смертельного травматизм (и на объемы бурения и масштаб добычи) снизились почти вдвое. Вместе с тем риск гибели нефтяника вырос примерно на 20% (см. рис. 5).
Динамика показателей смертельного травматизма в нефтедобыче (рис. 5) указывает, что в начале 2010-х гг. нефтегазодобывающая отрасль вышла из периода восстановительного роста и вошла в относительно стабильный производственно-технологический режим («период насыщения»). В таком состоянии заметные количественные изменения возможны, как правило, только с существенными качественными подвижками как в непосредственно производственно-добычной сфере, так и в области обеспечения промышленной безопасности опасных производственных объектов нефтегазодобывающей промышленности. Долгосрочно планируемая сейчас модернизация добычи нефти и газа должна быть не только технологически инновационной, но и безопасной (практически все инновации первоначально встречаются «в штыки» из-за неизвестности порождаемых ими «непонятных» опасностей). Но и нежелательные сценарии «затухающей деиндустриализации» отрасли тоже требуют особого обеспечения промышленной безопасности в такие периоды (по опыту спада отрасли в начале 1990-х гг.).
Для относительно стабильных, динамически устоявших систем поднадзорных опасных производственных объектов традиционные показатели аварийности и травматизма вполне пригодны, в достаточной степени представительны для формирования соответствующей «карты опасностей». Если же основная производственная деятельность претерпевает существенные качественные и количественные изменения (особенно актуально при реализации импортозамещения в НГК), то абсолютные показатели аварийности и травматизма необходимо дополнять риск-ориентированными показателями опасности аварий.
Риск-ориентированный подход – выявление, анализ и прогнозирование опасностей промышленных аварий, оценка риска и возможных масштабов последствий аварий на опасных производственных объектах для оптимизации необходимых организационно-технических мер предупреждения аварий, недопущения возникновения угроз крупных промышленных аварий и повышения эффективности обеспечения промышленной безопасности на отдельном опасном производственном объекте и (или) в системе поднадзорных объектов в целом
Опасности промышленных аварий и особенно возможности катастрофических последствий крупных промышленных аварий могут достаточно быстро перерастать в реальные угрозы технологической стагнации для социально-экономического развития любой индустриальной страны. Поэтому все промышленно-развитые страны создают, обслуживают и совершенствуют национальные системы обеспечения промышленной безопасности и подсистемы предупреждения угроз крупных промышленных аварий. Каждая действенная система безопасности первоначально исходит из текущих и постоянно обновляемых представлений о структуре существующих опасностей. Уже на основе имеющейся «карты опасностей» определяются возможные меры безопасности (предупреждения и/или локализации опасностей и угроз), выделяются необходимые или оптимально распределяются доступные ресурсы для сдерживания перерастания потенциала опасностей в реальность угрозы причинения масштабного и (или) непоправимого ущерба. От состояния и качества исходной «карты опасностей» (ее актуальности, масштабности, динамичности, наглядности и т.п.) во многом зависит результативность всей системы обеспечения безопасности, а также эффективность защищаемой от опасностей деятельности в целом. На этих общих закономерностях базируется и российское нормативно-правовое обеспечение промышленной безопасности, отражающее приоритетный принцип предупреждения наиболее опасных проявлений аварийности и травматизма в системе поднадзорных опасных производственных объектов. Обширные знания для предупреждения катастрофических последствий в значительной степени накапливаются из трагического опыта происшедших аварий. Помимо недопущения прошлых просчетов и ошибок, в современных условиях возрастания угроз реализации крупных промышленных аварий требуется систематизированное выявление, анализ и прогнозирование известных и новых аварийных опасностей в быстро изменяющейся промышленности, и особенно в ее базовой и наиболее опасной топливно-энергетической части – на объектах ТЭК и смежных отраслях промышленности, для которых «фактические неизбежна» реализация программы импортозамещения, особенно в части используемых современных инновационных машин и оборудования для добычи и переработки нефти и газа.
* * *
В заключении отметим ключевые особенности обеспечения промышленной безопасности в условиях реализации программ импортозамещения машин и экспортовозмещения энергии и сырья в новой РФ:
1. Проблема импортозамещения и экспортовозмещения – прямое следствие результатов реформ 1990‑х гг. по деиндустриализации России. Сильнее всего пострадало отечественное машиностроение, продукция которого была быстро вытеснена импортом на отечественном рынке НГК под действием анестезии «нефтяной иглы».
2. В отечественном НГК существенно изношены (морально и физически) основные фонды и кадры их обслуживающие. В машиностроении ситуация еще хуже (сокращение производственного потенциала машиностроения – деградация парка металлорежущих станков, демонтаж производства «крови машин» подшипников, сворачивание подготовки кадров машиностроителей и т.д.). НГК не может быстро и всецело заместить весь импорт в требующихся машинах и оборудовании – чревато тяжелыми авариями, ввиду объективно «отсталого» состояния в целом российского машиностроения (за немногими исключениями в ВПК). Поэтому в НГК необходимо не «среднее», а точечное ипортозамещение с обязательным усилением надзора за безопасным проведением работ при вводе инновационной отечественной техники в эксплуатацию (и с адекватным задаче кадровым обеспечением).
3. В сфере промышленной безопасности в основном сохранилось ядро норм безопасности, «заточенное» под отечественную технику: нормы «пишутся кровью аварии», и большинство этих трагических записей были сделаны в позднесоветский период расцвета отечественного машиностроения и НГК, а последующая реформа технического регулирования лишь изуродовала «советские нормы», снабдив их другими обертками заголовков, названий и форм утверждения.
4. Для конструктивной реализации импортозамещения в НГК (и экспортовозмещения сырья и энергии для промышленности в целом) потребуется «тонкая настройка» действующих требований безопасности. Стабильные режимы гораздо безопаснее переходных и пусковых (рано или поздно никуда не деться России от новой индустриализаций или реиндустриализации для создания отечественной гипериндустрии). Ростехнадзором уже подготовлены основные механизмы «тонкой настройки» правил безопасности. Главный из них – обоснование безопасности ОПО при «точечном отступлении» от норм с обязательным внедрением инновационных компенсирующих мер безопасности. К сожалению, бизнес много, и как оказалось впустую, говорил, что «отсталые» правила безопасности мешают ему модернизировать отечественную промышленность. В должной степени внедренное Ростехнадзором обоснование безопасности бизнесом для технологической модернизации производств не используется, как декларировалось.
5. По определению «всегда консервативные» требования безопасности не обеспечивают лучших решений, а оберегают от худших. Сегодня нельзя скатиться к вульгарному ура-импортозамещению (умалчивая о необходимости перенаправления экспортных потоков энергии и сырья для внутреннего потребления импортозамещающейся РФ), – для нашей страны требуется действенное и главное БЕЗОПАСНОЕ импортозамещение и экспортовозмещение – поступательное и спланированное насыщение НГК отечественными машинами и оборудованием, а промышленности российской энергией и сырьем, причем с обязательным прогнозом угроз новых аварийных опасностей и компенсирующими (и традиционными, и инновационными) мерами обеспечения промышленной безопасности.
Другие статистические данные о состоянии российской промышленности см. здесь>> А.И. Гражданкин, С.Г. Кара-Мурза. Белая книга: промышленность и строительство в России 1950–2014 гг. /Центр изучения кризисного общества. М.: Научный эксперт; М.: ТД Алгоритм, 2016. - 224 с.
Источник: |